The Rise of Robotics in US Manufacturing: Opportunities and Challenges in the US
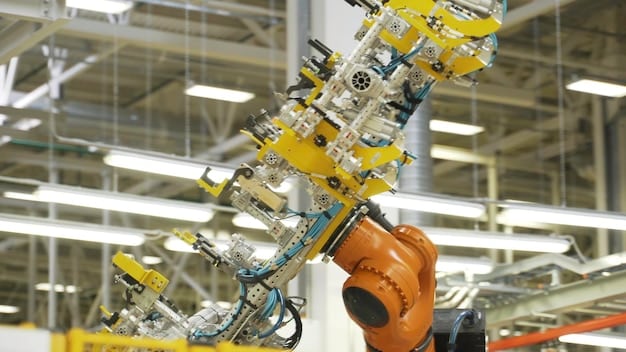
The Rise of Robotics in US Manufacturing: Opportunities and Challenges presents a transformative wave reshaping industries, offering enhanced productivity and efficiency while raising concerns about job displacement and the need for workforce adaptation.
The landscape of US manufacturing is undergoing a significant transformation with The Rise of Robotics in US Manufacturing: Opportunities and Challenges. This evolution promises to redefine production processes, but understanding its impact is crucial for navigating the future of work.
Understanding the Robotics Revolution in US Manufacturing
The integration of robotics into US manufacturing is not merely a technological upgrade; it represents a fundamental shift in how goods are produced, distributed, and consumed. This section provides an overview of the key aspects of this revolution.
The Evolution of Robotics in Manufacturing
Robotics has come a long way from simple automated tasks. Modern robots are equipped with sensors, AI, and machine learning capabilities, allowing them to perform complex operations with greater precision and adaptability.
Current State of Robotics Adoption
While some sectors have fully embraced robotics, others are still in the early stages of implementation. Factors such as cost, training requirements, and regulatory hurdles influence the pace of adoption across different industries.
- Enhanced Productivity: Robots can work continuously without fatigue, significantly increasing production output.
- Improved Quality: Automation reduces human error, leading to higher quality and more consistent products.
- Reduced Costs: Over time, robots can lower labor costs and minimize waste, contributing to long-term savings.
In conclusion, the robotics revolution in US manufacturing is transforming industries, driven by advancements in technology and the need for greater efficiency and quality.
The Opportunities Presented by Robotics in US Manufacturing
Robotics offers numerous opportunities for US manufacturing, ranging from increased efficiency and productivity to the creation of new high-skilled jobs. This section explores these benefits in detail.
Boosting Productivity and Efficiency
One of the primary advantages of robotics is the ability to automate repetitive and labor-intensive tasks, freeing up human workers for more strategic and creative roles. This leads to significant gains in productivity and efficiency.
Improving Quality and Consistency
Robots can perform tasks with greater precision than humans, reducing errors and ensuring consistent quality in products. This is particularly important in industries where accuracy is critical, such as aerospace and medical device manufacturing.
- New Job Creation: Robotics generates demand for engineers, technicians, and data scientists to design, maintain, and operate robotic systems.
- Economic Growth: Increased productivity and innovation drive economic growth, creating new opportunities for businesses and workers.
- Reshoring Initiatives: Robotics can make US manufacturing more competitive, encouraging companies to bring production back to the United States.
In conclusion, the opportunities presented by robotics in US manufacturing are vast, offering the potential for increased productivity, improved quality, and economic growth.
The Challenges Associated with Robotics Implementation
While robotics offers significant benefits, its implementation in US manufacturing also poses several challenges. This section addresses these concerns and explores potential solutions.
Job Displacement and Workforce Transition
One of the biggest concerns is the potential for job displacement as robots automate tasks previously performed by human workers. Addressing this challenge requires proactive measures to retrain and upskill the workforce.
High Initial Investment Costs
The initial investment in robotic systems can be substantial, particularly for small and medium-sized enterprises (SMEs). Financial incentives and support programs are needed to help these companies adopt robotics.
- Ethical Considerations: As robots become more autonomous, ethical considerations arise regarding their use and decision-making capabilities.
- Data Security: Increased automation leads to greater reliance on data, raising concerns about cybersecurity and data breaches.
- Skills Gap: Many manufacturers struggle to find workers with the skills needed to operate and maintain robotic systems.
In conclusion, addressing the challenges associated with robotics implementation in US manufacturing requires proactive measures to mitigate job displacement, reduce investment costs, and ensure ethical and secure use of robotic technologies.
Strategies for Successful Robotics Integration
Successful integration of robotics into US manufacturing requires careful planning and execution. This section outlines key strategies for maximizing the benefits of robotics while minimizing potential risks.
Workforce Development and Retraining Programs
Investing in workforce development and retraining programs is essential to prepare workers for new roles in the age of automation. These programs should focus on developing skills in areas such as robotics maintenance, programming, and data analysis.
Government Support and Incentives
Government support and incentives can play a crucial role in promoting robotics adoption, particularly among SMEs. This includes tax credits, grants, and loan programs designed to offset the initial investment costs.
- Collaboration: Fostering collaboration between industry, academia, and government can accelerate innovation and the development of new robotic technologies.
- Focus on Human-Robot Collaboration: Designing robotic systems that work alongside humans, rather than replacing them, can improve productivity and reduce job displacement.
- Continuous Improvement: Robotics implementation should be viewed as an ongoing process of continuous improvement, with regular evaluation and adjustments.
In conclusion, successful robotics integration in US manufacturing requires a comprehensive strategy that addresses workforce development, provides government support, and promotes collaboration and continuous improvement.
The Future of Robotics in US Manufacturing: Trends and Predictions
The future of robotics in US manufacturing is poised for continued growth and innovation. This section explores emerging trends and provides predictions for the years ahead.
Advancements in Artificial Intelligence and Machine Learning
AI and machine learning will play an increasingly important role in robotics, enabling robots to perform more complex tasks with greater autonomy and adaptability. This will lead to the development of more intelligent and versatile robotic systems.
Increased Use of Collaborative Robots (Cobots)
Cobots are designed to work alongside humans, providing assistance with tasks without the need for extensive safety measures. The use of cobots is expected to increase significantly as manufacturers seek to improve productivity and flexibility.
- Robotics-as-a-Service (RaaS): RaaS models allow companies to access robotic technologies without the high upfront investment costs, making robotics more accessible to SMEs.
- Digital Twins: Digital twins, virtual replicas of physical assets, will be used to optimize robotic systems and predict potential maintenance issues.
- Sustainability: Robotics will play a role in promoting sustainable manufacturing practices by reducing waste, conserving energy, and improving resource efficiency.
In conclusion, the future of robotics in US manufacturing will be shaped by advancements in AI, increased use of cobots, and emerging business models such as RaaS, driving innovation and sustainability.
Case Studies: Successful Robotics Implementation in US Manufacturing
Examining real-world examples of successful robotics implementation can provide valuable insights for manufacturers considering adopting robotic technologies. This section highlights several case studies.
Case Study 1: Automotive Industry
A US automotive manufacturer implemented robotic welding systems to improve the quality and efficiency of its production line. This resulted in a significant reduction in defects and increased production output.
Case Study 2: Food Processing Industry
A food processing company used robotic packaging systems to automate the handling and packaging of perishable goods. This reduced labor costs and extended the shelf life of its products.
- Aerospace Industry: An aerospace manufacturer implemented robotic drilling and fastening systems to improve the precision and quality of its aircraft assembly process.
- Electronics Industry: An electronics company used robotic assembly systems to automate the production of circuit boards, reducing manufacturing time and improving quality.
- Medical Device Industry: A medical device manufacturer implemented robotic sterilization systems to ensure the safety and compliance of its products.
In conclusion, these case studies demonstrate the diverse applications of robotics in US manufacturing and the potential benefits for companies across various industries.
Key Aspect | Brief Description |
---|---|
🚀 Productivity Boost | Robots enhance output and reduce downtime. |
🤖 Workforce Changes | Retraining needed for new roles. |
💰 Investment Costs | Significant upfront expenses. |
🛡️ Ethical Issues | Need careful planning for ethical concerns. |
Frequently Asked Questions
▼
Robotics in manufacturing enhances productivity by automating tasks, improves quality through precision, and reduces operational costs by minimizing waste and needing less labor.
▼
While robotics can displace some jobs, it also creates new opportunities in areas like robotics maintenance, programming, and data analysis, requiring a shift in workforce skills.
▼
The challenges include high initial investment costs, the need for skilled workers to manage and maintain robots, and addressing ethical or safety concerns related to their use.
▼
Industries such as automotive, aerospace, food processing, electronics, and medical device manufacturing can substantially benefit from using robotics due to increased efficiency and precision.
▼
Manufacturers should invest in workforce development programs that focus on robotics, seek government support and incentives for adoption, and foster collaborations to share knowledge and resources.
Conclusion
In conclusion, The Rise of Robotics in US Manufacturing: Opportunities and Challenges presents a transformative shift, offering enhanced productivity and efficiency. While challenges such as job displacement and high costs exist, strategies like workforce development and government support can pave the way for successful integration. Embracing these changes will be crucial for US manufacturers to remain competitive in the global economy.